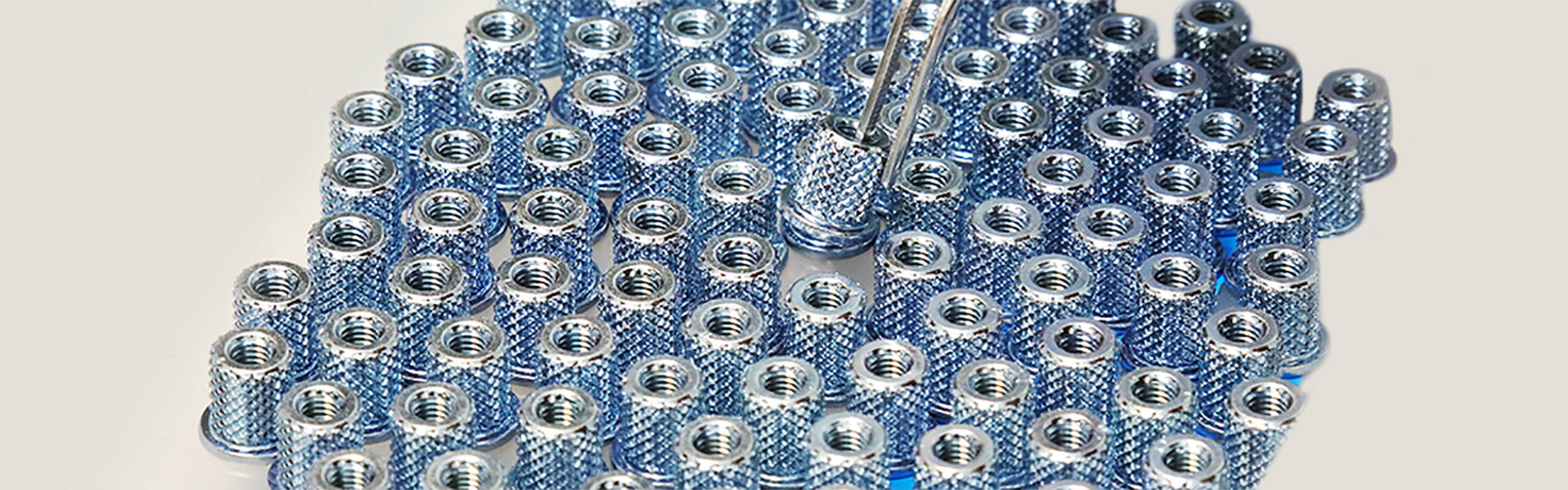
STRENGTH
Comprehensive production system that spans all processes, from design to processing to quality control
We conduct all of our manufacturing processes In our company, which allows us to provide high-quality products that meet our customers’ needs in a short time frame. We have all of the equipment we need for each process in our own factories, and work on design alongside the production sites, continually accumulating expertise so that we can continue providing high-level quality and technologies to our clients.
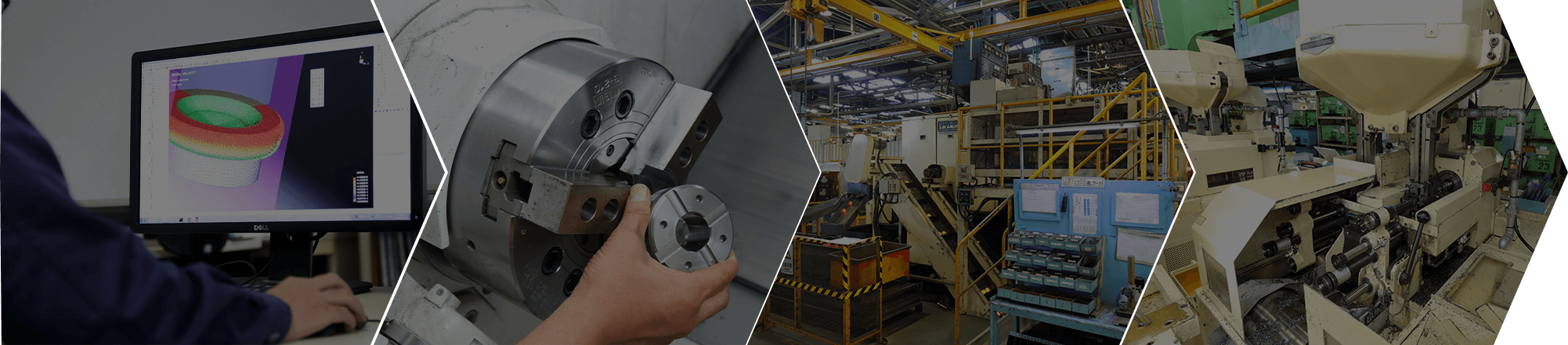
-
STEP 01
Design
-
STEP 02
Mold
making -
STEP 03
Forging
-
STEP 04
Threading
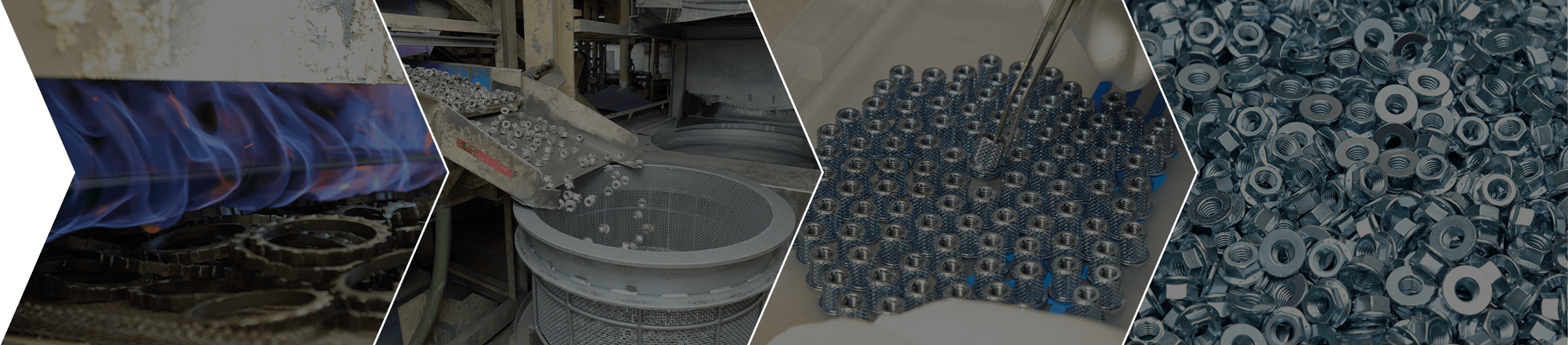
-
STEP 05
Heat
Processing -
STEP 06
Surface
Processing -
STEP 07
Inspection
-
STEP 08
Shipment
Manufacturing structure in coordination
with Japan’s largest automobile manufacturer
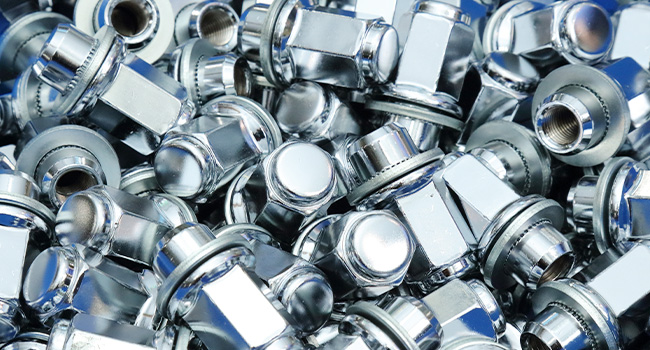
We have worked with Japan’s largest automobile manufacturer since our inception, and worked continually to meet their high-level requirements. And by refining our technological ability and providing high-quality, short turn-around, low-priced products, We are able to continuously achieve numerous awards. We continue to grow within the automobile industry as well as various other industries.
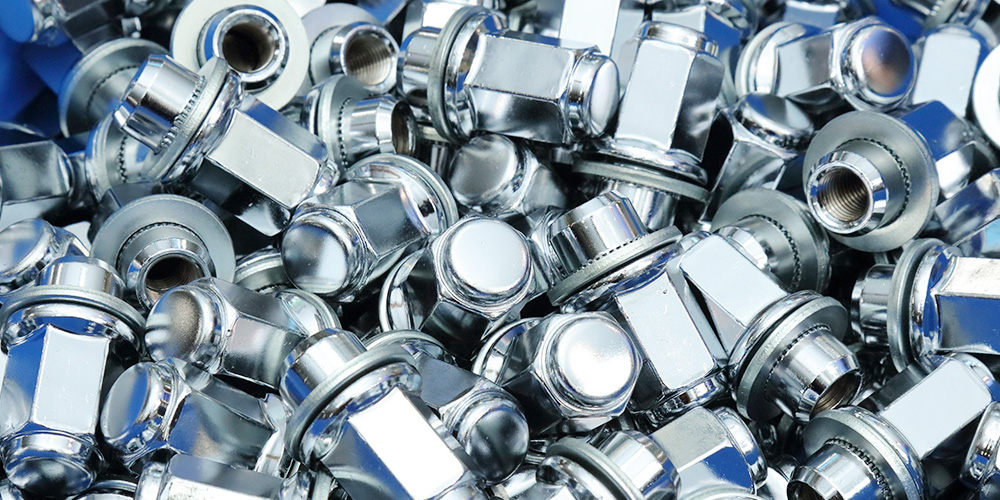
Product processing that
suits client needs
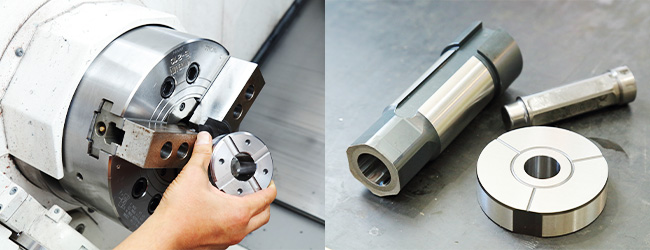
It is no exaggeration to say that the quality of nuts and bolts are determined by the quality of their metal molds. Here at Sugiura Seisakusho, we work with the production sites to design the metal molds, which allows us to meet the various needs of our clients. Most fastener manufacturers outsource the manufacture of their metal molds. We, however, manufacture about 50% of our metal molds In our company, which allows us to manufacture a wide variety of components at low costs.
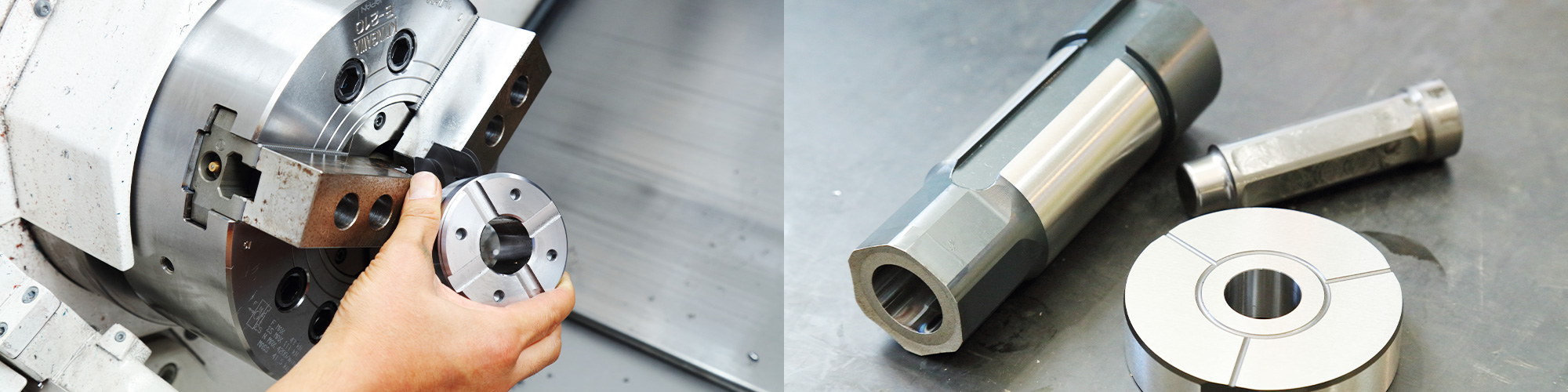
TECHNOLOGY
We manufacture a wide variety of components using our three main forging technologies (cold forging, heat forging, and warm forging), as well as secondary processing machines for processes like threading and machining. We also conduct our own heat processing and surface processing to meet client needs.
Cold Forging
Cold forging is a processing method wherein room temperature metal is placed under pressure to form certain shapes. It is used to manufacture primarily high-volume items (about M3 - M22), whether nuts or bolts.
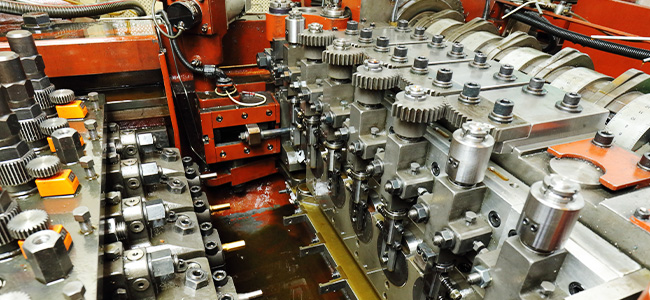
Heat Forging
Heat forging is a processing method wherein metal, heated to 1,000 - 1,200 degrees Celsius and softened, is placed under pressure to form certain shapes. It is used primarily to manufacture large nuts (M22 - M100).
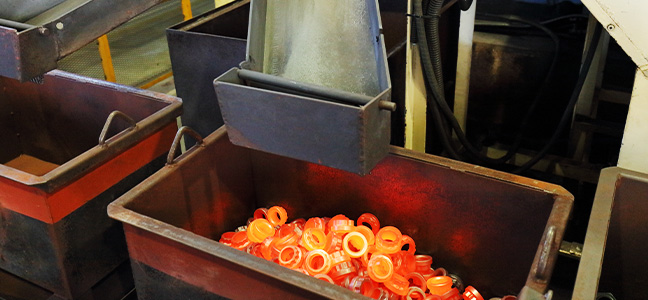
Warm Forging
Warm forging is a processing method wherein metal, heated to about 500 degrees Celsius and softened, is placed under pressure to form certain shapes. It is used primarily to manufacture stainless steel components that are not suited for cold forging.
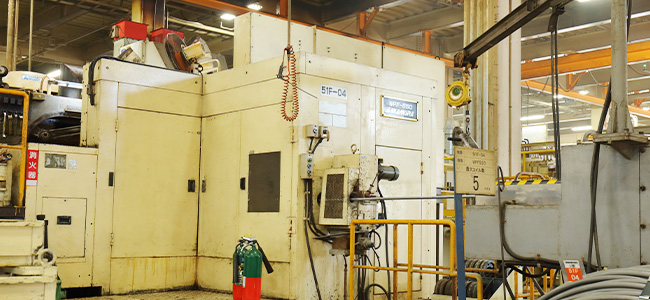
Threading
Threading is a form of processing where grooves are engraved onto nuts and bolts. Here at Sugiura Seisakusho, we have accumulated screw cutting expertise since immediately after our inception, and we use it to determine the optimal specification for each of our products.
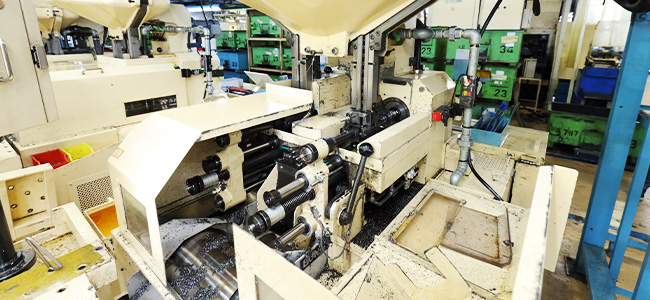
Machining
Cutting machines are used for more precise processing of forged components, etc. Here at Sugiura Seisakusho, we have worked continually to refine our machining technologies, and are able to manufacture high value-added components suited for various industries.
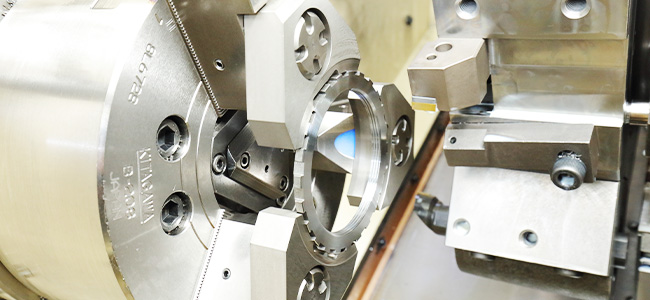
Heat Processing / Surface Processing
Heat processing is used to increase the strength and rigidity of processed components.
Depending on customer need, we also conduct surface
processing--for example, with zinc plating, GEOMET, etc., for anti-corrosion properties.
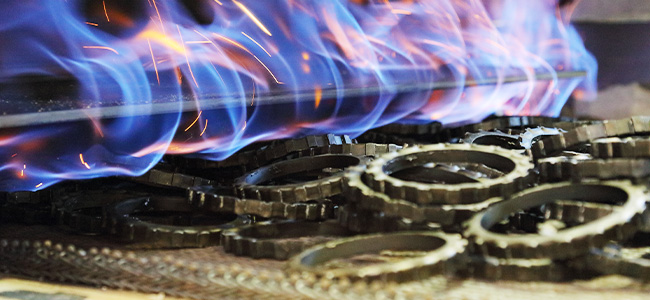
QUALITY
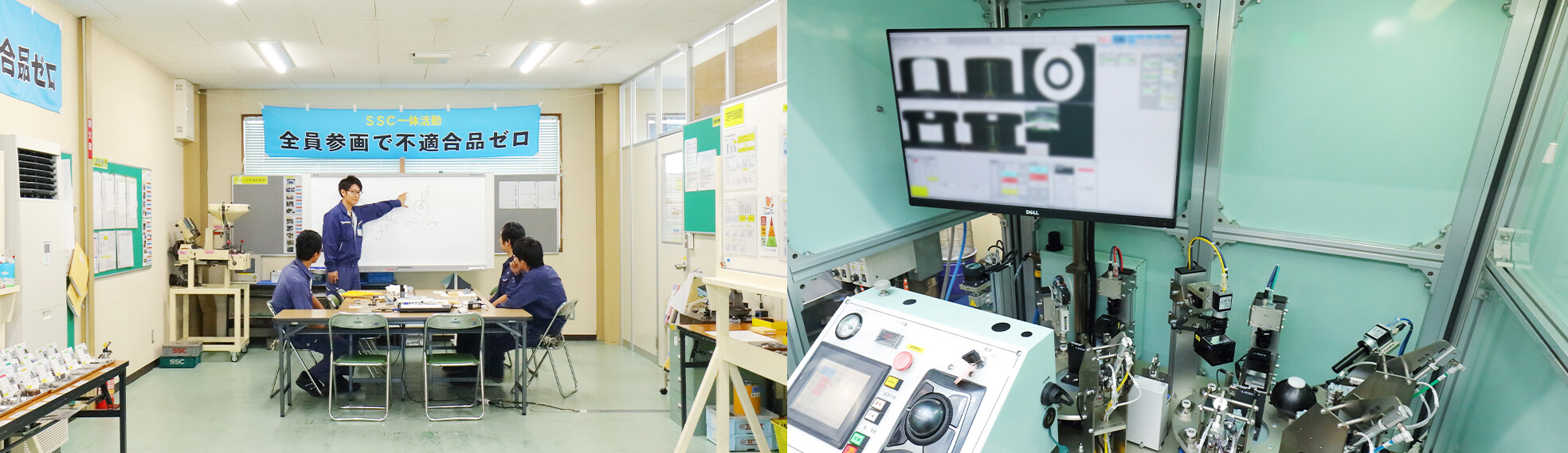
Our Inspection System
The processed products are evaluated via various types of inspection equipment, in order to ensure a high level of quality.
We also have a system in place to guarantee the smooth delivery of over 300 million products a month.
Thorough and Meticulous Quality Control Training
Nuts and bolts are simple components. However, if a defective nut or bolt is installed in an automobile, it can lead to a major
accident--which is why we put our employees through thorough and meticulous quality control training.
We also have what is called a “Quality Dojo,” where we reflect on in-process inspections and past defects, and reinforce our complete, everyday commitment to quality.
ENVIRONMENT
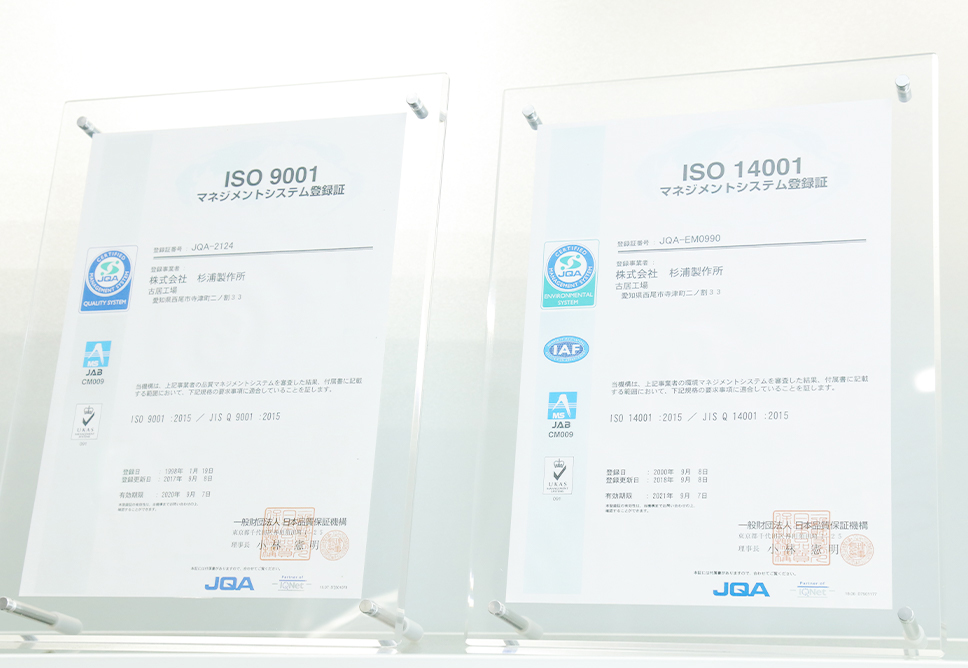
Eco-friendly equipment
that is kind to
the environment
and the surrounding areas
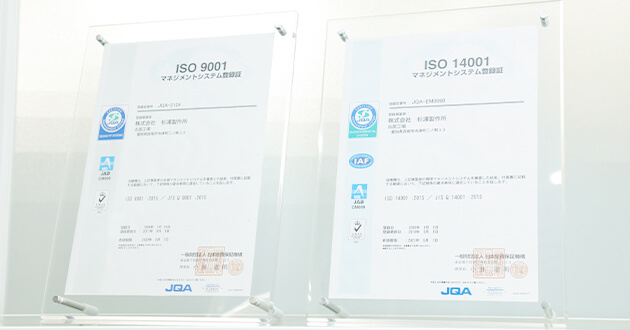
We make various efforts to be kinder to the environment, whether it be switching to a type of heat treatment burner that utilizes town gas, to reducing the amount of carbon emissions, to reducing our environmental impact by upgrading deteriorated equipment.
We are also committed to the community, taking measures to reduce the amount of noise in our factories, for the sake of the surrounding neighborhoods.
We acquired ISO 14001 Certification in 2000, and will continue working on a daily basis towards systems that are kinder to the global environment and to the surrounding areas.
Better working
environment
for our employees
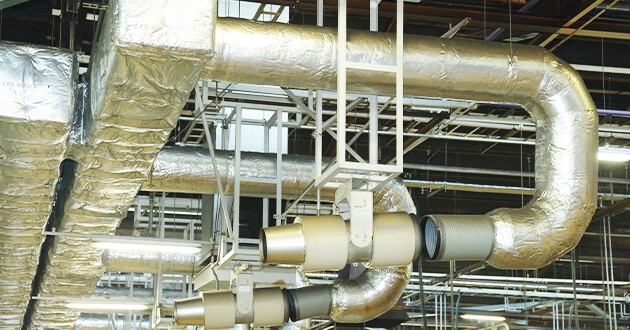
We are working to provide safer environments for our employees by establishing pedestrian zones within factory grounds, improving processes for high-elevation work, etc. We have also taken measures to improve productivity by implementing large-scale air conditioning units to help prevent potential health risk such as heat stroke.
Our focus is on improving the working environment so that our employees can work comfortably and more effectively.
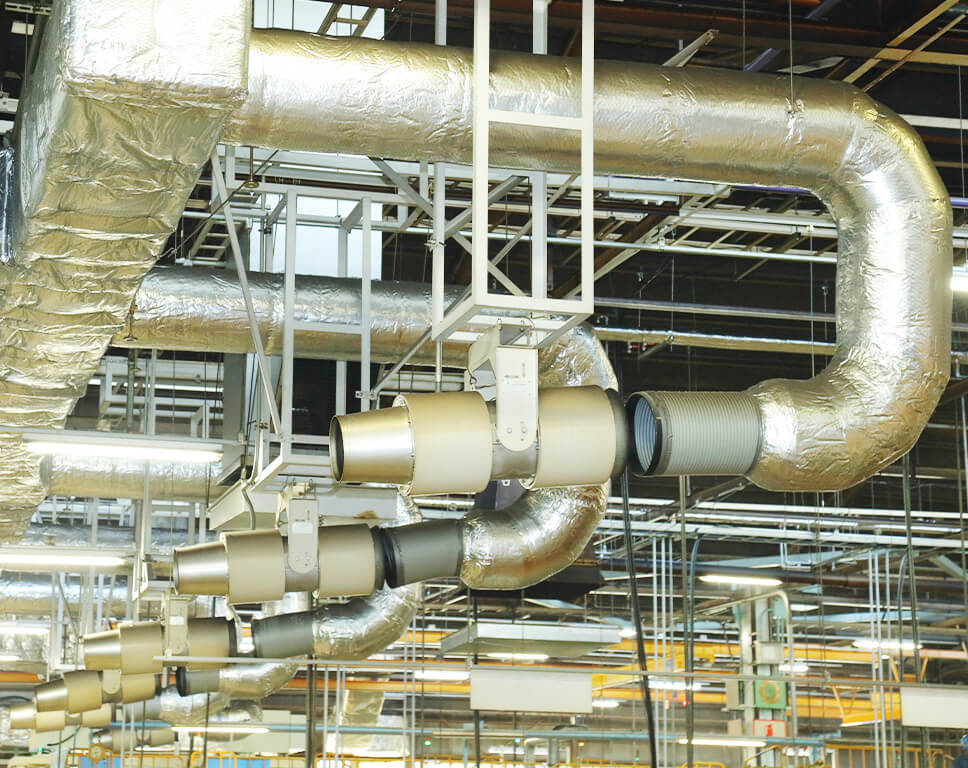